Because Cleaner is Better for Business
Jebsen & Jessen Packaging’s new biomass boiler in Vietnam is supporting business growth while reducing our carbon footprint
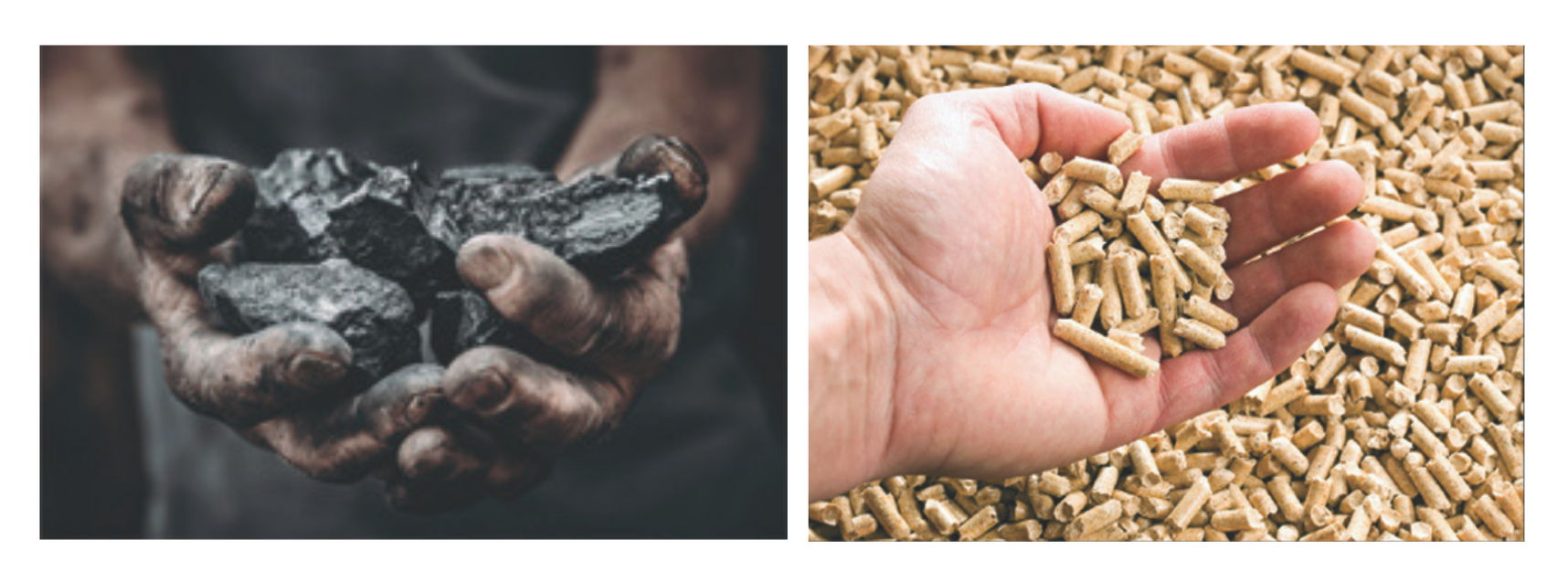
Jun 2019- As a Group, we are the first industrial company in South East Asia to achieve 100% carbon neutrality. Our commitment to caring for the environment is embedded in our daily operations in many ways, the latest of which is a new biomass boiler for Jebsen & Jessen Packaging’s moulded foam factory in Que Vo, Vietnam — the first of its kind in the country.
This clean-energy replacement for our conventional coal boiler burns sustainably-sourced wood pellets, which do not produce harmful CO2 emissions, while increasing our steam capacity by 20% to support growing demand from customers. By reducing our reliance on coal, we are now able to reduce our carbon footprint by an estimated 11,440 tons a year and better serve our customers!
Our Journey from Coal to Biomass
For the Packaging team in Vietnam, it took eight years of commitment and prudence to realise their vision of replacing coal with biomass fuel. When the decision to do so was taken in 2012, the team had planned to retain its existing coal boiler and simply swap coal with wood pellets. The trial, which took place over the next few years, produced a number of obstacles.
The lack of a steady supply of biomass fuel was resolved when the team managed to convince the building contractor to invest in a start-up to produce wood pellets, and supported the company in overcoming difficulties in boosting production.
However, fuel productivity and equipment efficiency remained a challenge. Working with the supplier, they made several hardware improvements, such as replacing the undersized crusher and upgrading the pellet press machine. Despite their best efforts, the boiler, which was originally designed for coal, could barely achieve 70% efficiency in burning biomass. Their target was 85%.
In 2018, the team invested in a biomass boiler instead. After a successful trial run in March 2019, the biomass boiler went into full operational mode in April, thereby:
• Reducing our carbon footprint by an estimated 11,440 tons a year
• Increasing our steam capacity from 10 tons to 12 tons to support business growth
• Enhancing our production capacity as the old coal boiler room has since been converted into a production platform
The boiler has since passed third-party certification checks and efficiency evaluation with flying colours, well exceeding the local authority’s requirements.
The Business Case for Renewable Energy
All over the region, our Group seeks to use renewable energy whenever possible. JJ-Lapp’s new cable factory in Tangerang, Indonesia, MHE-Demag’s new crane factory in Santo Tomas, Philippines, and Jebsen & Jessen Packaging’s existing foam factory in Nilai, Malaysia will all be fitted with rooftop solar panels.
These require significant capital expenditure but as an investment in the future of our Group and our environment, we believe that the returns will be just as significant.
“Our customers, particularly multi-national companies, are happy to see this green initiative. Even though biomass does cost us more in terms of operating expense, it is a good demonstration of our value of commitment — to contributing to a greener environment to benefit people and partners,” said Tau Siong Chui, Regional Managing Director, Jebsen & Jessen Packaging.